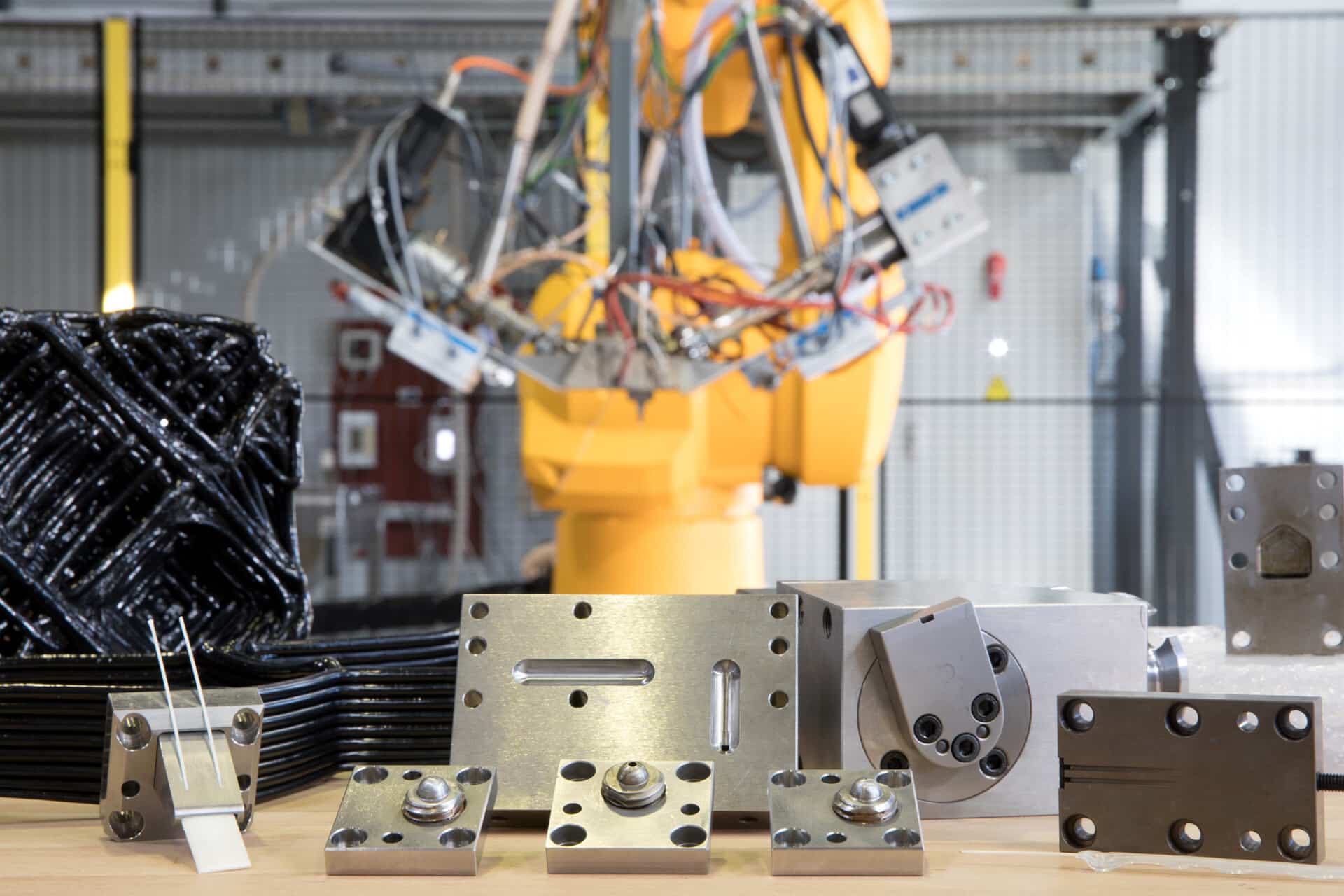
Mechanics, digital processes and materials
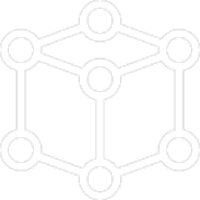
Materials & Processes
PROJECTS
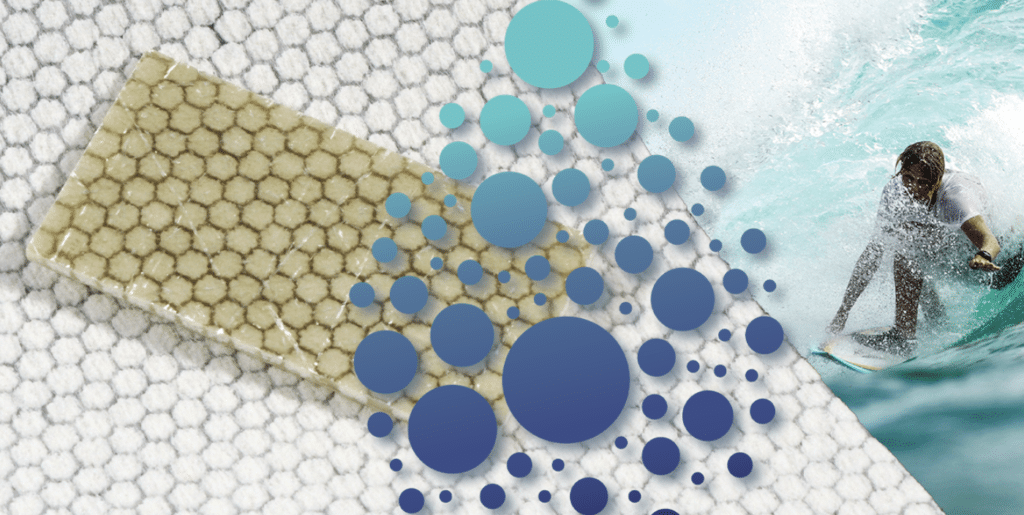
SEABIOCOMP project
SEABIOCOMP project
The SEABIOCOMP project aims to develop new 100% bio-based composite materials in order to reduce carbon footprints, particularly for industrial applications in marine environments. For this project we have developed bio-based polymer non-woven preforms (e.g., PLA) and flax fibres, ready…
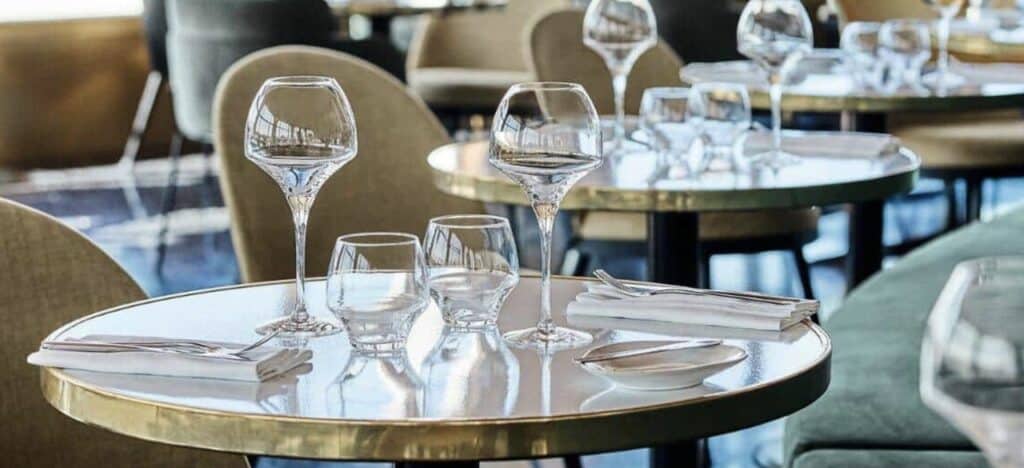
IMT NE – Arc R&D
IMT NE – Arc R&D
IMT Nord Europe – Arc R&D Research Partnership: Development of innovative systems for the production of glass items dedicated to tableware The overall objective of the ARC France – IMT Nord Europe partnership is to develop innovative systems for the…
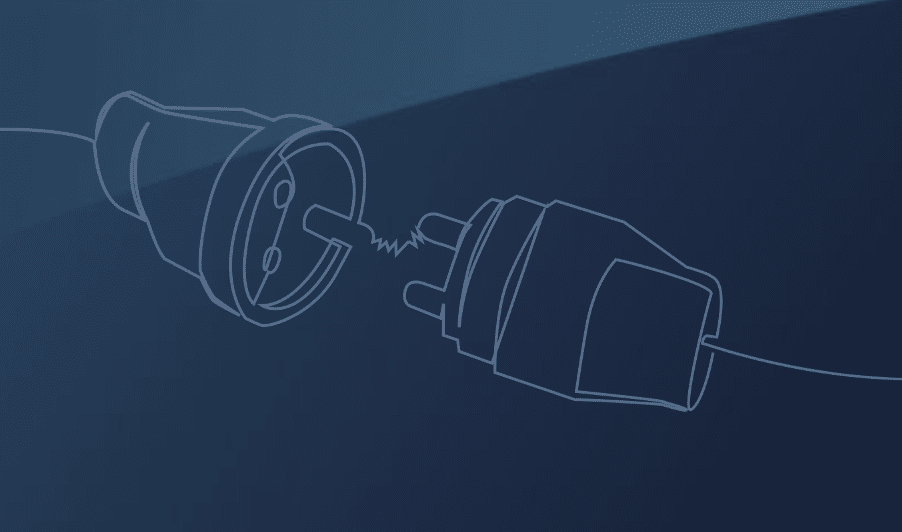
ESARIS partnership
ESARIS partnership
ESARIS partnership: advanced materials, design, electromechanical and thermal engineering, industrial processes. In 2022 Institut Mines-Télécom (IMT) and Esaris Industries signed a strategic partnership for R&D and training to assist this industrial midcap with its development and strategic diversification of its…
Want to learn more about
"Mechanics, digital processes and materials" ?
Our teams at the IMT Nord Europe research centres are here to help
CONTACT US