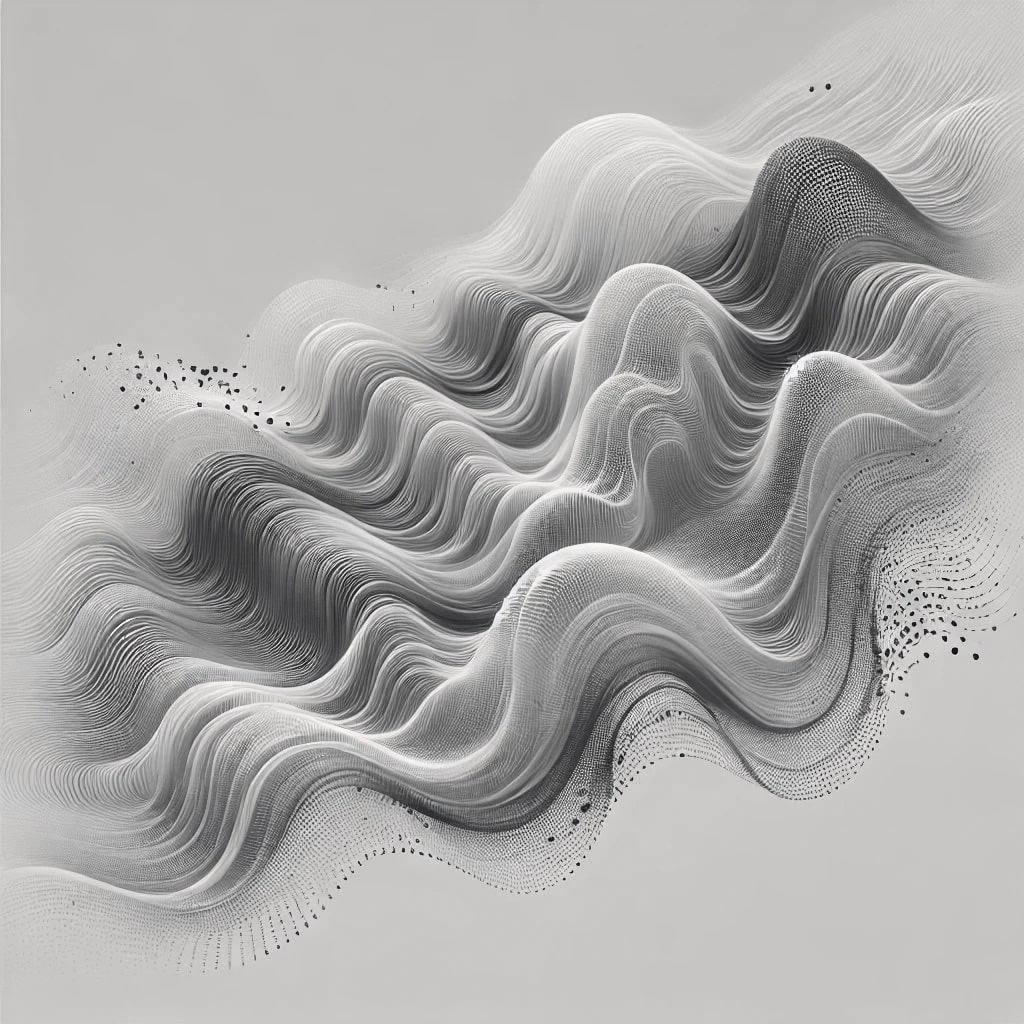
MISSA
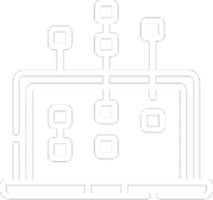
Digital Systems
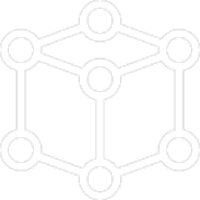
Materials & Processes
Want to learn more about
"MISSA" ?
Our teams at the IMT Nord Europe research centres are here to help
CONTACT USDigital Systems
Materials & Processes
The MISSA project focuses on numerical modelling of two-phase flows in heterogeneous domains. The key challenging aspect is that the heterogeneity will be assumed to have features of a size much smaller than that of the simulation domain. The moving interface between the two phases will hence develop a complex morphology at a very small scale during the simulation. Numerical modelling of these phenomena is of great interest to the manufacturing industry as they may cause the formation of microscopic void defects in industrial parts, which then have a severely deteriorated performance. For instance, in resin transfer moulding of fibre-reinforced composites, the resin flows progressively at a coarse scale inside the mould, but the presence of the preform leads to the formation, deformation and migration of bubbles at a fine scale between fibres. Void defects are likely to remain trapped between the fibres at the end of the impregnation.
When the fine scale is much smaller than the coarse scale, it is not computationally feasible to construct a single numerical model where both scales are discretized together. For instance, in the case of resin transfer moulding, it is not feasible to create a Finite Element (FE) mesh that would cover the mould and simultaneously capture each fibre. To tackle this challenge, the two scales will be separated in this project, and an original homogenization theory will be developed. This project will go beyond existing theories which mainly address steady single-phase flows, in order to treat unsteady two-phase flows with surface tension and obstacles at the fine scale. This new multiscale theory will be implemented as an FExFE (or FE²) computational homogenization algorithm. It will be possible to predict and visualize simultaneously the flow at the two scales. The theory and its implementation will be validated by comparison with single-scale simulation results for academic examples of increasing complexity.
With respect to simulating more complex and industrially realistic problems, the computational cost of the proposed FE² approach will be limiting. Indeed, at each time step of the simulation, it will be necessary to solve a nonlinear problem for the coarse scale, and also a huge number of nonlinear problems at the fine scale, corresponding to each integration point of the coarse scale mesh. In the project, the partial repetitiveness of the fine scale calculations will be exploited to reduce their computational cost by several factors of magnitude. This will be achieved by first constructing a database of fine scale simulation results, and then using an auto-encoder, which is a deep learning neural network designed to construct nonlinear Reduced Order Models (ROMs). The relevance of this deep learning approach will be quantified by comparison with principal components analysis, which is a linear reduced order modelling approach that has been widely used in the recent literature. In order to make predictions and integrate this nonlinear ROM in the FE² algorithm, two research tracks will be investigated: a purely deep learning-based regression and a hybrid approach. In the first method, another deep learning neural network will be trained to predict the reduced unknowns of the nonlinear ROM from the boundary conditions of the fine scale problems. In the second method, fine scale flow equations and boundary conditions will be written in terms of the reduced unknowns and solved to make predictions.
The most efficient method in terms of generalization (accuracy on unseen data) and computation time will be integrated in the FE² algorithm to create an original FExROM algorithm. It will be interesting to see if some three-dimensional industrial applications are enabled by this algorithm thanks to its reduced computational cost compared to FExFE and single-scale approaches. Simplified examples inspired from resin transfer moulding and additive manufacturing will be investigated.
Funders: Agence Nationale de la Recherche (ANR) – AAPG 2022 – CE46 ‘Modèles numériques, simulations, applications‘’ – Programme ‘’Jeunes Chercheuses et Jeunes Chercheurs‘’ (JCJC)
Partners: IMT Nord Europe (CERI MP et CERI SN), National University of Singapore
Winner: Modesar SHAKOOR
Our teams at the IMT Nord Europe research centres are here to help
CONTACT US