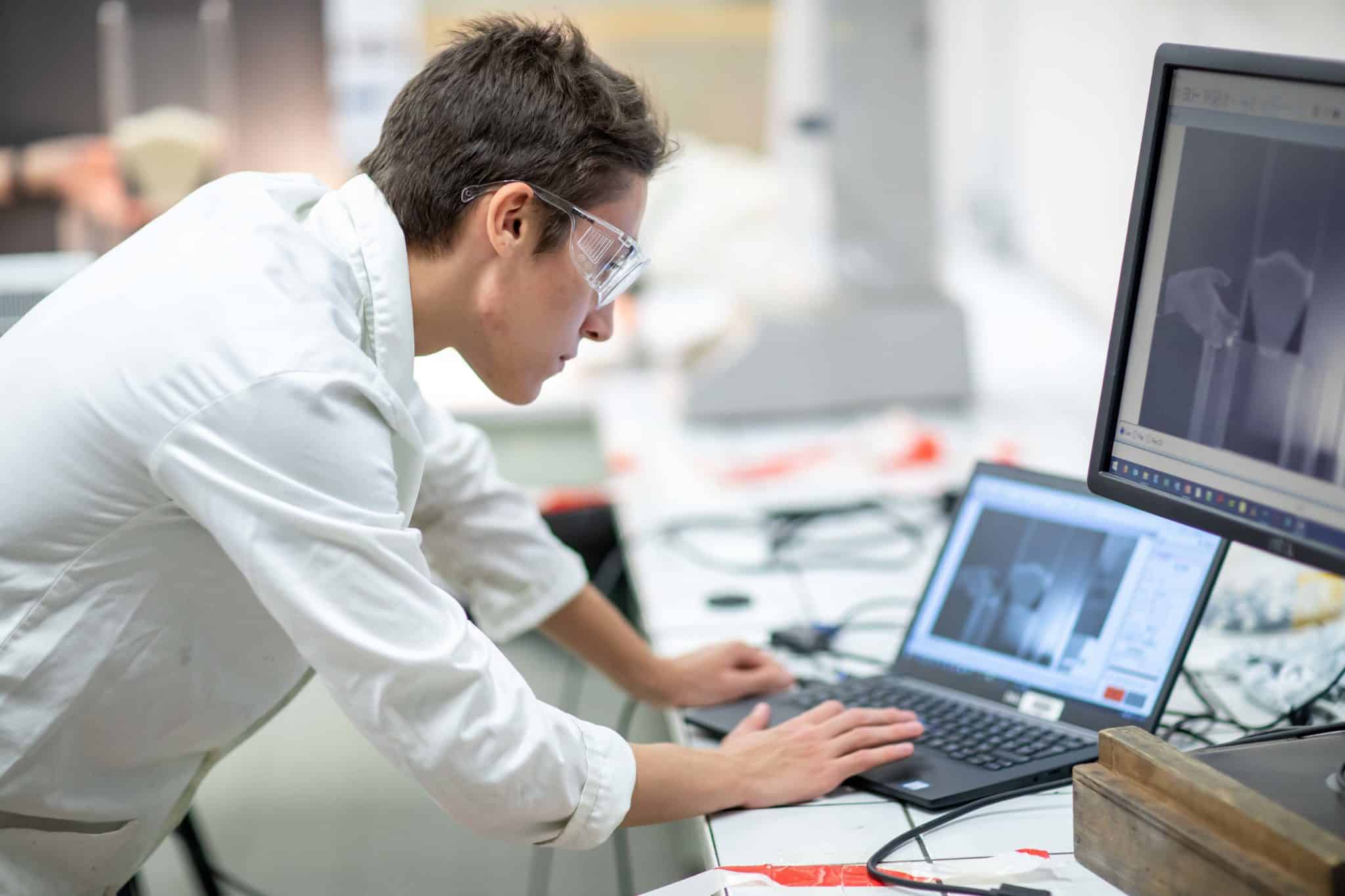
NEO Chair
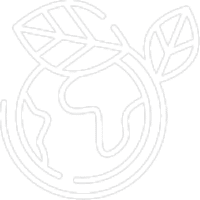
Energy Environment
NEO stands for “Numerical and Experimental Optimisation platform for efficient design of automotive heat exchangers”
The performance of exchangers is directly related to the geometry of the solid parts, the structure of thermal convection flows and conductive/convective transfers. Based on technical expertise comprising three areas of scientific development – design by numerical simulation of passive intensification techniques, implementation of numerical shape optimisation techniques, and experimental characterisation at different scales (laboratory model, prototypes of significant size), CERI EE helps develop new types of heat exchangers with improved thermal and airflow performance, thus reducing operating costs and improving the energy efficiency of systems. The technical solutions developed include the structuring of exchange surfaces to control and enable the spatio-temporal manipulation of swirl flow structures, optimisation of surface extensions by integrating conductive/convective coupling, and control of turbulent transition phenomena, with the aim of increasing transfers by minimising losses caused by mechanical dissipation.
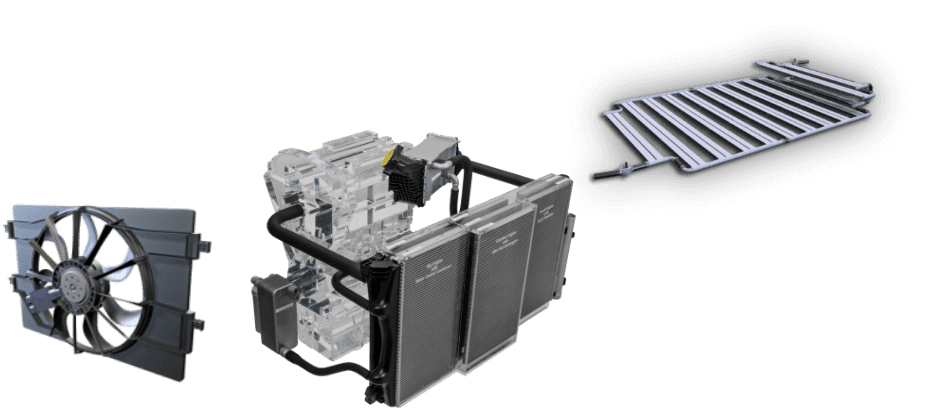
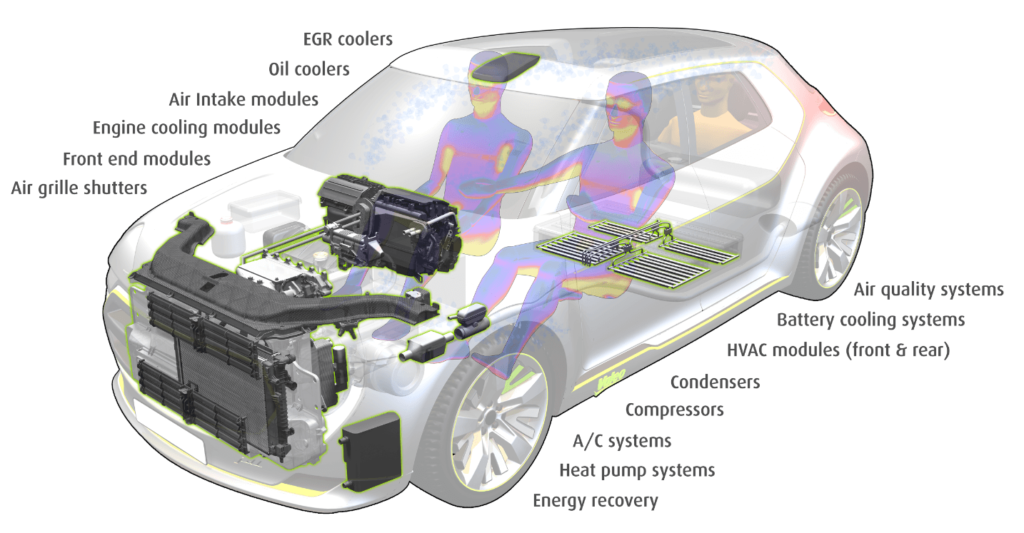
Design of passive intensification techniques by numerical simulation
This area of research aims to improve and optimise the structuring of fluid flows and its efficiency. It focuses primarily on the geometry of the channels integrating the elements for producing swirl dynamics, for example, which play a decisive role in improving transfer and mixing performance. The innovative channels we wish to study will have specially designed exchange surfaces equipped with macro and micro-structures. The millimetric-sized macro-structures to be placed on the exchange surfaces, the fins (gas flow side) and the liquid flow channels, have a considerable impact on the efficiency of the embedded exchanger components.
The micro-structures (a few tens of microns in size) are surface structures that can be produced using various machining processes or surface deposits. These micro-structures are also the result of conventional exchange surface manufacturing methods, which, due to tool imperfections and wear phenomena, create small geometric variations on the exchange surfaces. In the end, these micro-structures, whether they are intentional or the result of geometrical variations from industrial processes, have considerable effects on turbulent transition phenomena, heat transfers, pressure loss reduction and corrosion and fouling phenomena.
Development of topological optimisation techniques
This aspect relates to the implementation of numerical topological optimisation techniques. Applying this type of optimisation to conductive/convective transfers is a major innovation. Initially developed in solid mechanics, it has only recently been developed in the fields of fluidics and heat science and its scope is still very limited in these areas. Compared to parametric optimisation and surface optimisation techniques, which use adjoint solver, the topological optimisation method is particularly relevant because it does not use any predefined hypotheses about the geometry of the system. In other words, topological optimisation approaches any starting geometry by treating each grid cell as a degree of freedom independent of the system, which is a very important step in creating optimal exchangers, as compared to parametric optimisation, which establishes a starting geometry. Another key point is that it enables use of the entire computational domain volume to find an optimal solution for the allocation of the material. This second area of research aims to design a digital conductive/convective topological optimisation platform interacting with an open source CFD code to treat complex anisothermal flow configurations such as embedded exchangers. The main purpose and advantage of developing and using this innovative optimisation approach is to provide decisive assistance in the design of geometries for intensified exchangers. Since this type of optimisation produces results that are inherently free of predefined hypotheses, they will provide a base of solutions for intensification techniques which researchers can then draw from to develop the geometries of VALEO exchangers. It is also important to remember that additive manufacturing using metallic and polymer materials allows for the development of geometries which were previously impossible using standard manufacturing methods, and which fit perfectly with the optimal shapes created by topological optimisation.
Development of experimental methods for identifying thermal and dynamic fields
This third research area concerns the development of advanced experimental metrological methods for the phenomenological analysis of physical mechanisms and the experimental validation of digital simulations. Validating the geometric solutions and intensification techniques studied is indeed a crucial step. CERI EE possesses the expertise and measurement techniques and methodologies required for the detailed analysis and performance qualification of different types of thermal components with complex geometries. The measurement systems used include infrared thermography and stereoscopic particle image velocimetry (SPIV) techniques. The laboratory also develops the methods (inverse mathematical techniques) which must be associated with these advanced measurement techniques to obtain and identify flow and thermal fields, which are fundamental data for analysing convective transfers.
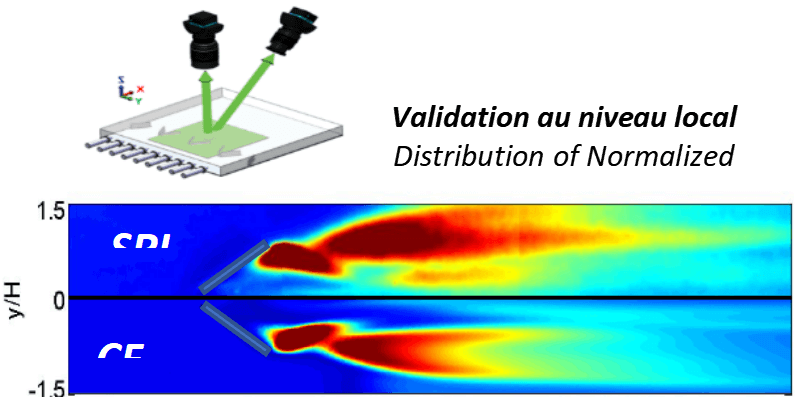
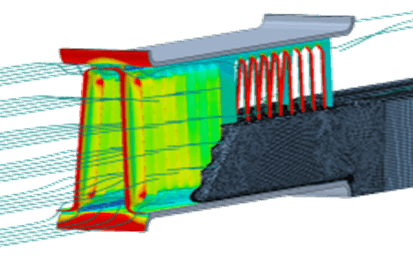
Want to learn more about
"NEO Chair" ?
Our teams at the IMT Nord Europe research centres are here to help
CONTACT US